Stapelweise Baumstämme lagern auf dem Gelände von ARS Starkholzplatten. Sie alle kommen aus einem Umkreis von 30 Kilometern rund um das Werk in Roßhaupten im Allgäu. WBV, FBG, Holzhändler und kleine Familienbetriebe bringen das PEFC-zertifizierte Holz dorthin – ARS- und HRW-Chef Andreas Reßle kennt seine Lieferanten alle persönlich.
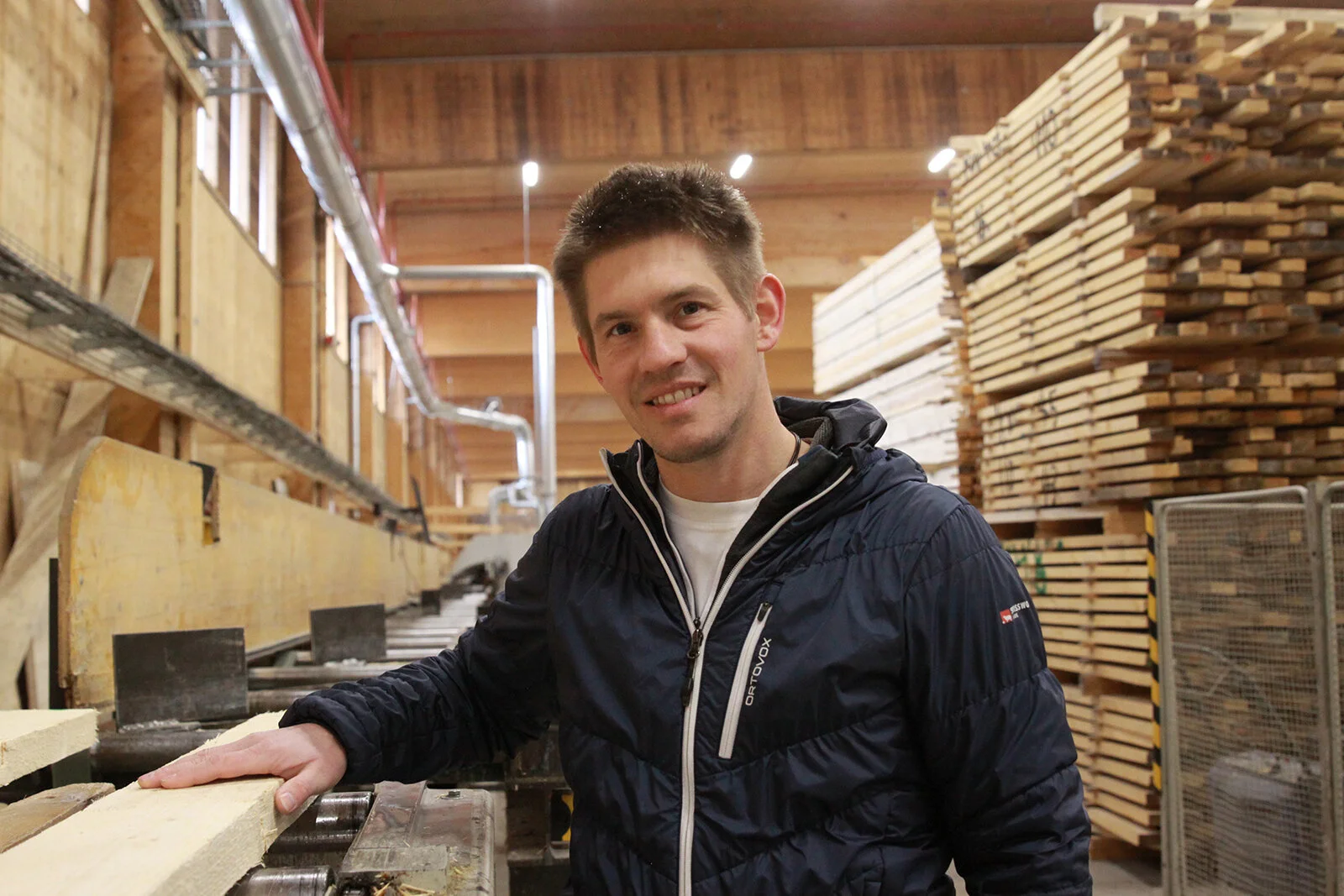
Seine Zimmererlehre und den -Meister hat Reßle im elterlichen Betrieb HRW gemacht, 2009 hat er seinen eigenen Betrieb gegründet. Seitdem treibt er die Entwicklung und den Einsatz von Vollholzwänden unermüdlich voran. In erster Linie, weil sie nachhaltig sind, aber auch, “weil Holz einfach ein schöner Baustoff ist”, sagt er. “Es ist schön zu bearbeiten, es ist warm – aber natürlich kommt es auch darauf an, was man daraus macht“.
Reßles Unternehmen kann heute neben den zehn Zentimeter dicken Wänden für den HOME mit einem patentierten Verfahren und eigens dafür gefertigten Maschinen Wände aus massivem Holz bauen, die bis zu 54 Zentimeter dick sind.
„Diese Extremfälle sind Sonderanfertigungen für Einsatzbereiche, in denen Beton nicht mehr funktioniert, weil es sich nicht mehr trägt“, sagt Reßle, der in einer der vier großen Massivholzhallen auch gern selbst mit anpackt und Platz schafft für die Ladung, die ein Mitarbeiter mit dem Gabelstapler heranfährt.
Für die Entwicklung und Weiterentwicklung seiner Vollholzwände arbeitet er mit Handwerkern, Wissenschaftlern der Technischen Unis in Dresden, Wien und München und verschiedenen Prüflaboren zusammen.
Die Wände werden im Heißpress- und Hochdruckverfahren bei 95 Grad Celsius miteinander verleimt. „Bei dieser Temperatur sind zur Verarbeitung des Leims keine umweltschädlichen Zusätze erforderlich, die später ausgasen“, sagt Reßle. „Das macht die Wände zu einem idealen Baustoff für Allergiker, Kindergärten und alle möglichen empfindlichen Bereiche.“
Doch bis es soweit ist, dass das Holz zu massiven Wänden verarbeitet wird, dauert es einige Wochen. Nach dem Einschneiden müssen die Holzpakete zunächst sechs bis acht Wochen lufttrocknen. Im Anschluss kommen sie für eine Woche in eine Wärmekammer. Dort werden sie erhitzt, sodass der Holzkern konstant eine Temperatur von 60 Grad hält.
Schon bei 53 Grad Celsius werden die Eiweißverbindungen im Holz aufgespalten: Sie sind es, die Insekten und Schädlinge in das Material locken. Nach ein paar Tagen in der Wärmekammer ist von dem Eiweiß nichts mehr übrig – und das Holz ist für Würmer und andere ungebetene Gäste dauerhaft uninteressant.
Zugleich beträgt die Feuchtigkeit im Holz nur noch rund sieben Prozent, „so viel wie später im Wohnraum“, sagt Reßle. Die Wärmekammer selbst erhitzen er und seine Mitarbeiter mit Sägespänen und anderen Holzresten der Produktion – 99 Prozent eines Baumstammes werden hier im Werk verarbeitet und genutzt.
Die Holzpakete aus der Wärmekammer sortieren Mitarbeiter nach ihrer Optik: besonders gleichmäßige und ebene Stücke verwenden sie für die äußeren Lagen, Bretter mit natürlichen Färbungen finden ihren Einsatz in der inneren Schicht der zehn Zentimeter dicken Wand des HOME-Mikrohauses.
Nach der Sortierung werden die Deckbretter und die Mittellage maschinell angeordnet, verleimt, nach der Heißverpressung optisch kontrolliert, gegebenenfalls ausgebessert und geschliffen. Mithilfe moderner Fräsen schneiden die Mitarbeiter die Wände eines jeden HOME-Mikrohauses inklusive Fenster- und Türöffnungen millimetergenau zu.
In einem Raum, dessen Wände aus Vollholz sind, heizt man laut Reßle automatisch zwei bis drei Grad weniger. “Durch die Masse entsteht eine Phasenverschiebung”, sagt er. “Es dauert ewig, bis Wärme da durchwandert.” Es gibt aber noch einen anderen Grund, ist er sich sicher: “Das ist ein psychologischer Effekt. So ein Raum ist einfach gemütlich und vermittelt Wärme.”
Präzise von Andreas Reßle und seinem Team vorbereitet, geht es für die Wände nach Nürnberg. Dort werden sie zum fertigen Modulhaus zusammengebaut. Mehr dazu hier in Kürze!